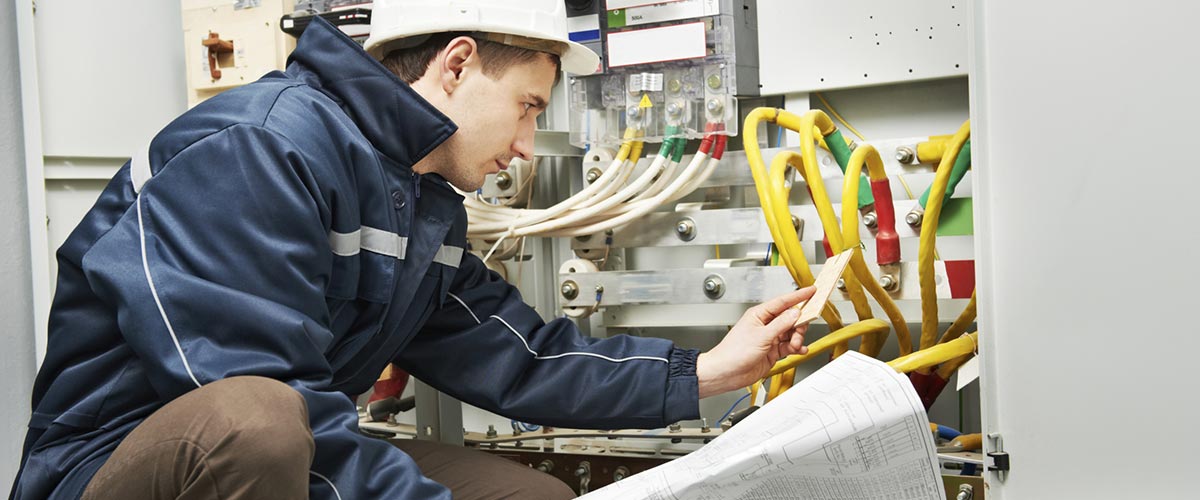
SERVICING THE ADELAIDE HILLS IN SAFETY TESTING
Frequently Asked Questions
Why should I test and tag my electrical equipment?
Electricity is one of the biggest dangers in the workplace, and the failure to maintain and service electrical equipment places employees’ lives at risk. The Occupational Health and Safety Act places a "duty of care" on employers to provide a safe workplace. Preventive maintenance, with regular electrical safety checks, is the ideal way to avoid unnecessary and unfortunate accidents, as well as the legal ramifications that follow.
How often do I have to get my equipment tested?
What does testing and tagging involve?
Visual inspection:
The most important test is a 'visual inspection' of the item, especially focusing on the lead. Cords should be firmly anchored in plugs and connections should be made solidly with no frayed ends. Insulation should be undamaged, and copper terminals should be clean and not pitted.
Electrical testing:
The appliance will be tested with various test equipment to check for any unseen electrical faults. These tests include insulation resistance, earth continuity, earth bond, correct polarity, and current leakage.
Record keeping:
A comprehensive 'asset register' is generated which shows all items tested. This includes item description and location, test results, tag number, and faulty items recommendations/actions. A "Certificate of Compliance' is included showing the sites tested and the standards complied with.
Tags:
A safety tag must be placed on the appliance verifying its compliance. This tag must clearly display the name of the tester or test company and the date tested and retest date.
What equipment needs to be tested?
Any appliance within a business that has a flexible cord that plugs into either a single-phase 240V power outlet or 3-phase 415V power outlet needs to be tested. These appliances include anything from computers to toasters or drills to factory machinery. Any appliance within the workplace that is portable and not hardwired needs to be regularly tested. This is to adhere to Occupational Health and Safety regulations, and comply with Australian Standards AS/NZ 3760.
What is AS/NZS 3760?
This is a document written by Standards Australia that specifies the procedures and criteria for the in-service safety inspection and testing of electrical equipment, which is designed for connection by a flexible cord. It also applies to cord extension sets, portable outlet devices, residual current devices and portable isolation transformers.